Why Now is the Right Time for Business Process Mapping
The past few months has shown us that we don’t always have to have employees on site to carry on our business. However, since many businesses shifted their employees to work virtually without a whole lot of preparation, amidst a crisis, the way things were done may not always be the best option. Now that remote work will be the new normal for many businesses it is a good time to explore how to optimize the way we work and discover opportunities to improve our business operations.
A good place to begin is by taking a fresh look at your entire business and business processes.
This is where process mapping comes in. Simply put, process maps form the blueprint of how your business works. They are visual representations of various key business processes in your company. They enable you to see how each process and step works and are interrelated.
Once prepared, visual process maps will enable you to identify and eliminate obsolete processes, reduce waste, and remove constraints that get in the way of productivity. All this naturally leads to better resource use, better customer quality and customer service, cost reductions and enhanced profitability.
Process mapping methodologies
There are many. Six Sigma, Lean methodologies, Total quality management and the Theory of Constraints are some of them. Each has its own way of doing things and different types of documentation.
- Six Sigma uses a data-driven approach to help you improve process and business performance and helps reduce waste and defects.
- Lean manufacturing, or Lean for short, shows you how to systematically minimize waste in your business processes and to do so without compromising productivity.
- TQM or Total Quality Management aims to improve customer quality by using an organization-wide focus on continuous improvement.
- Just-in-time (JIT), often referred to as Toyota System Production, focuses on reducing your inventory costs by ensuring that stock buildups are avoided, saving money clogged up unnecessarily in working capital.
- Theory of Constraints says that we all operate within constraints. It offers a systematic approach to finding and eliminating the key constraints in your business processes. Once the most pressing constraint is resolved, you move on to the next most pressing one.
This is by no means an exhaustive list.
And then there are the combinations. Many practitioners prefer to use a combination of methodologies—such as Six Sigma+Lean—to give you a comprehensive understanding of how your business processes operate and interact. At AccountFWD we prefer to use a mix of tools for process mapping exercises to deliver optimum results for our clients.
Many Benefits of Process Mapping
Regardless of the methodology you choose, there are undisputed benefits to process mapping.
- Gives you a bird’s eye view of the business. Everyone can begin to see how things work because of the visual formats. Sure, you and your teams know how they work. Process mapping shows the big picture and how things are interrelated. This makes it easy to find solutions to pressing problems.
- Easier to pinpoint issues. Sometimes there may be issues that are complicated and spread across processes so that identifying the real issue becomes difficult. Working together on process maps helps your team work together to troubleshoot and find common solutions.
- Easy to eliminate unnecessary steps. As companies grow, leaders add on new procedures, processes, and staff. Same thing happens when processes are digitalized and upgraded. Over time, if you are not careful, you may end up with a tangled web of obsolete process steps that weigh down your productivity and waste employee effort and time and company resources. These will get highlighted in process maps.
- Easy to identify trouble spots and waste. Naturally this means cost savings and better productivity overall.
- Better employee engagement and moral. No one suffers more from process inefficiencies than the people who do the work. Getting employees involved in creating process maps makes them feel valued and improves morale. It is a definite win-win because we all support a world we help to create. Anyway, you can’t bring about changes on your own without team buy-in and involvement, can you?
- Shows and delivers results and changes become easier to implement. Typically, people are resistant to change. This is why making process changes may not always be welcomed with the enthusiasm. However, being able to show how processes like Six Sigma can improve quality, and how lean methods can cut down waste will help convert some of your teams. Others will be persuaded by the reductions of unnecessary steps and effort and improved productivity. It enhances their quality of work life and who doesn’t want that?
- Improves quality of communications across the entire business. When everyone is on the same page about how processes work and are interrelated, it will make it easier to break communication barriers between functions and find common solutions to issues that run across more than one business function or process.
- Process maps can be useful for the future and for employee training. Next time round, when you feel the need for review of your processes you will find it easier to do. When all processes are clearly mapped, you will find it easier to train new employees and get them appreciate their roles within the organization.
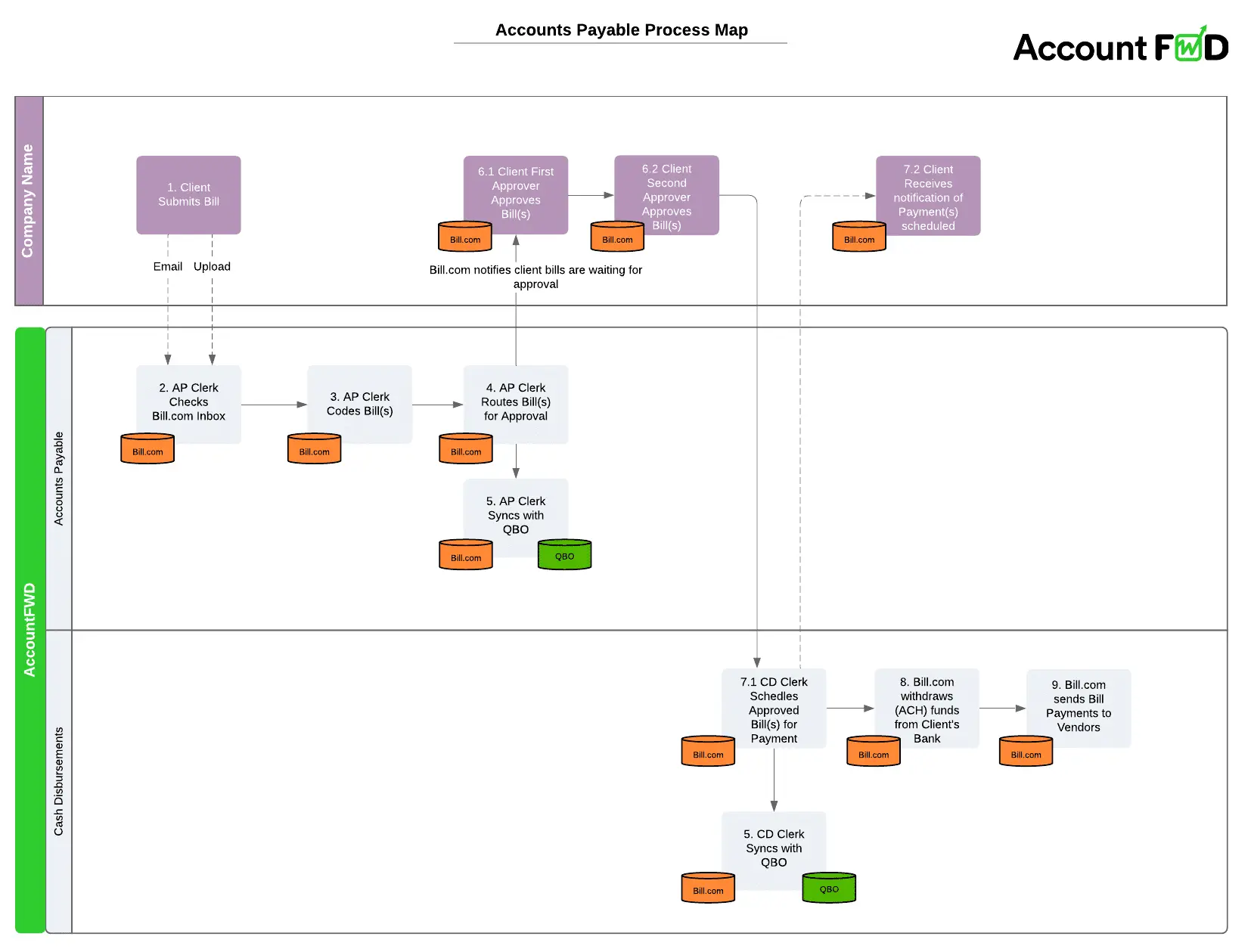
Why are we talking about process mapping now?
Now is the time for process mapping for many of our clients because they highlight the potential for improving quality, customer service, productivity, and profitability of their businesses.
Considering the uncertain economic situation we are all in, many firms are seeking ways to streamline processes and improve productivity especially in their recently established remote work environments. These companies wish to ensure that work flows smoothly without relying entirely on individuals to do the right thing. Business process mapping and the resulting potential improvements can help your business achieve this goal.
At AccountFWD we guide entrepreneurs through process mapping and process improvement projects. If you have questions about how business process mapping works, send us a note, schedule a time to connect, or give us a call 954-686-8687.